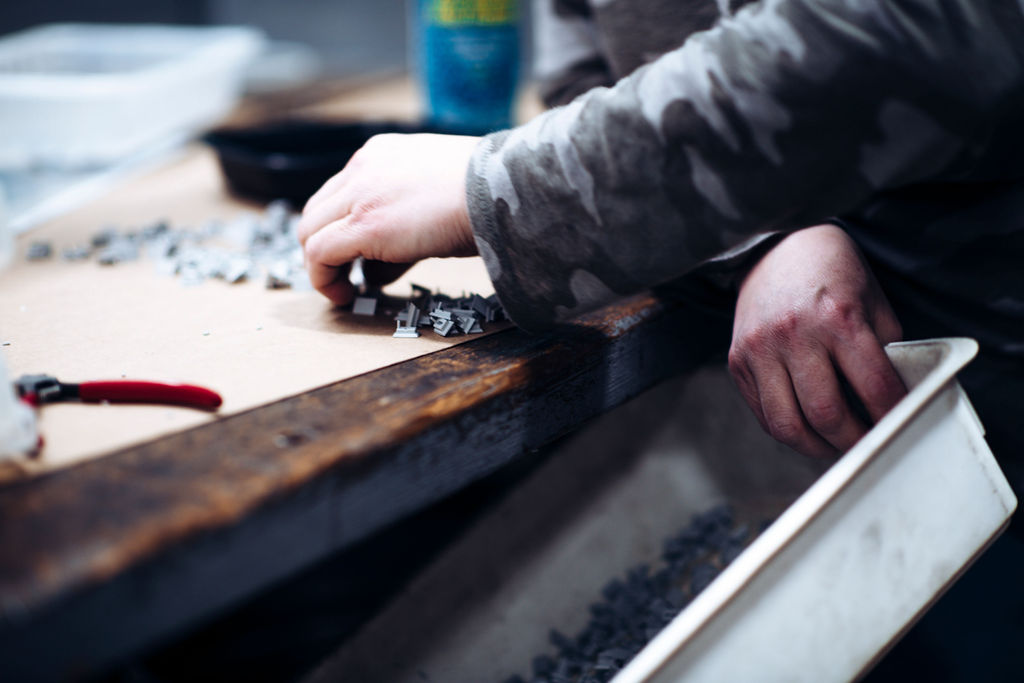
The 6th S. Kyle Tew
There are many basic principles & methodologies of manufacturing that evolve constantly. One of these concepts of Lean Manufacturing is a system of workplace organization called “5S”. 5S is a systematic approach to improve housekeeping and standardize processes making them more efficient while reducing waste for your team members. There are many benefits to 5S when implemented correctly. These benefits include increased productivity, improved quality, improved company image, heightened morale, better visual management, and improved safety.
The 5S’s:
1. Sort – Eliminate whatever is not needed by separating needed tools, parts, and instructions from unneeded materials.
2. Set in Order – Organize whatever remains by neatly arranging and identifying parts and tools for ease of use.
3. Shine – Clean the work area by conducting a cleanup campaign.
4. Standardize – Schedule regular cleaning and maintenance by conducting S’s 1-3 daily.
5. Sustain – Make 5S a way of life by forming the habit of always following the first four S’s.
This brings us to the 6th S. Some companies, managers, or consultants have added another S to their 5S method, which is Safety. The Safety step involves concentrating on what can be done to eliminate risks in work area by arranging items or cells in certain ways.
Most manufacturing professionals consider improved safety an inherent outcome of performing the other 5 S’s correctly, and as a result, say the sixth S is redundant and unnecessary. However, sorting out an area & removing any clutter will eliminate obstacles. With less items to trip over, catch fire, or cause other types of damage, safety level is consequently higher. A well-sorted workplace is a safer workplace. Wiping away dust, for example, removes a fire hazard. Cleaning up spills reduces the risk of slip-and-fall accidents. Hazards become apparent and visible in a clean and organized environment. Environments that follow organized standard processes are going to be safer environments. The longer the 5S methodology is followed, the safer the facility will be. Therefore, some believe if the workspace is properly organized & cleaned, a separate safety step is unnecessary.
Neither approach to 5S (6S) or safety is right or wrong. Safety should be the number 1 priority of every organization no matter the industry. The bottom line is no matter if an organization is looking to eliminate waste, improve productivity, or become a safer workplace; 5S is an excellent method to use, proving its effectiveness by thousands of companies around the world.